Global "carbon capture", a game of cost and energy consumption
01
Carbon Neutrality: Walking on "Two Legs"
In the pursuit of the "dual carbon (carbon peak, carbon neutrality)" goals, in addition to energy conservation and emission reduction, unblocking the energy storage link, and gradually replacing fossil fuel power generation with new energy sources such as wind and solar, there is a more direct method: to control and reduce the carbon dioxide that has been emitted and is currently being emitted as much as possible, and to achieve true "zero carbon" with "negative carbon technologies."
Originally, this matter did not need to be a concern for humans, as our planet Earth should be a planet with the ability to balance carbon. It can absorb and release a certain amount of carbon dioxide through forests, soil, rocks, and oceans over a longer period, keeping the atmospheric carbon dioxide content within a safe range of circulation.
However, the continuous growth of the population and the Industrial Revolution have disrupted this natural balance. Over the past century, the emissions of carbon dioxide and other greenhouse gases produced by human industrial activities have long threatened the ecological environment. The air is fair, and all of humanity is an undifferentiated community of shared destiny, which is why there is a global backdrop of "carbon neutrality."
Advertisement
It needs to be clarified that in the current process of achieving the "dual carbon" goals, the content of carbon dioxide in the atmosphere will continue to increase, but the rate of increase will slow down. Although the proportion of fossil fuels such as coal will be gradually compressed, they will not completely exit. Just like the electrochemical energy storage driven by new energy vehicles now, it is still unable to change the reality that coal power generation is the mainstay.
As Huang Jing, the director of the China 21st Century Agenda Management Center, said, even by 2060, under the strong inertia of fossil energy consumption, it will still be retained in a small proportion. "By 2060, fossil fuels in China will still account for at least about 19% of the primary energy consumption structure," and this part of the carbon emissions will need to rely on "negative emission" system engineering such as CCUS to artificially offset.CCUS is an Essential Negative Emissions Technology for the Future
CCUS (Carbon Capture Usage Storage) refers to the process of separating carbon dioxide from the atmosphere or from processes such as power generation, chemical industry, and steelmaking for utilization or geological sequestration. As mentioned, it is fundamentally different from the approach of reducing carbon emissions through the transformation of old and new kinetic energy, aiming instead to effectively control the existing "carbon" in the atmosphere.
Within the entire CCUS system, "capturing" carbon is just the first step, and "utilizing" carbon is the key point that makes this chain achieve commercial operation. However, carbon capture alone accounts for more than half of the total cost of CCUS projects. To clarify this chain, one must first understand the technological principles behind it.
02
High Technological Costs
On a desolate plain in Iceland, one can see 80 large fans and filters standing tall. When these giant fans, arranged in a "Z" pattern, are activated simultaneously, they produce a sound like flowing water. Invisible to the naked eye, carbon dioxide in the air is captured by the entire setup and sent underground, where it reacts with basalt to form stone, and is then permanently stored underground—this is the scene of the world's largest carbon capture plant, Mammoth, which has recently begun operation and started capturing its first batch of carbon dioxide.
This plant is the second large-scale Direct Air Capture (DAC) facility developed by the Swiss startup Climeworks. Under normal conditions, the plant will have an annual carbon dioxide capture capacity of up to 36,000 tons. Although this is a drop in the ocean compared to the global carbon dioxide emissions of 37.4 billion tons last year, in the future, there will be more than one "Mammoth."
Let's explain in detail how carbon in the air is captured. Based on the production process, carbon dioxide capture technologies can be divided into three categories: pre-combustion capture, post-combustion capture, and oxy-fuel combustion capture.
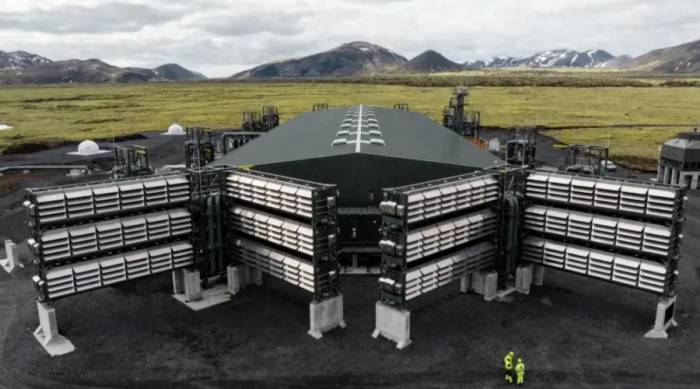
Pre-combustion capture technology refers to the process of transferring the chemical energy from carbon-based fuels before combustion, and then separating the carbon from other substances carrying energy, thus achieving the capture of carbon before combustion and utilization. For example, converting fuel into a gaseous mixture of hydrogen and carbon dioxide, where the hydrogen is separated and can be burned without producing any carbon dioxide, while the carbon dioxide is compressed for transportation and storage. However, readers familiar with hydrogen storage might understand that this pre-combustion capture technology involves fuel conversion steps that are too complex and not suitable for the application in coal-fired power plants.Oxy-fuel combustion capture technology can also be considered as capture during combustion. As the name suggests, it uses oxygen instead of traditional air with a high nitrogen content as the oxidant to burn fuel. This avoids the dilution effect of nitrogen, and the exhaust gases produced during combustion become pure water vapor and carbon dioxide. The water vapor condenses upon cooling, leaving behind a nearly pure stream of carbon dioxide, which means it is easier to separate and collect.
The development of more durable oxygen carriers can continuously reduce the cost of the CLC system.
Another cutting-edge technology is Chemical Looping Combustion (CLC), which also falls under the category of oxy-fuel combustion capture. Its working principle involves using metal oxides as solid oxygen carriers to split the combustion of traditional fuels in direct contact with air into two gas-solid reactions. In this way, fuels and air do not need to come into direct contact, and the regenerated metal oxides can be recycled in the combustor.
It is worth mentioning that China is also keeping pace with international peers in the third-generation capture technology route represented by CLC. In September last year, the world's largest 3-megawatt CLC carbon capture pilot device was established in Deyang, Sichuan. The device was jointly designed by French energy giant Total Energies, Dongfang Boiler, Tsinghua University, and other units, with a total investment of about 20 million euros. It is understood that while producing steam, the project can capture high-purity carbon dioxide and reduce the power supply efficiency loss caused by carbon capture from more than 10 percentage points to within 4 percentage points.
However, this technological route has not yet been put into large-scale commercial application due to its current immaturity and high costs. Involving a variety of complex chemical reactions and processes, it requires a large number of high-precision professional equipment, such as reactors, separators, heat exchangers, etc. The initial equipment setup for CLC alone is a high investment, plus R&D and maintenance costs. If it cannot form an economy of scale (hundreds of megawatts), then according to the calculation of the aforementioned CLC device, the cost of carbon capture could be as high as 100 USD/ton.
03
How to choose the landing environment?
In general, the industry currently favors and applies the "post-combustion capture" technology most widely, and DAC belongs to this field. According to different application scenarios, post-combustion capture is actually divided into direct capture from industrial emission sources and DAC. Different scenarios mean different participants, but from a technical principle perspective, there is not much difference between the two.Direct capture of industrial emissions refers to high-emission enterprises such as the State Energy Group, CNOOC, and Sinopec conducting capture on their own or engaging third parties to do so within their factories; the site selection for DAC (Direct Air Capture) is more flexible, and it does not need to deal with nitrogen oxides and sulfur compounds in industrial emissions, so the scale of the equipment can be large or small. However, both require an emphasis on carbon dioxide separation technology.
The general process of the DAC route involves two main technological paths for separating carbon dioxide, either from the flue gas after the combustion of fossil fuels or directly from the air: one is chemical solvent absorption, and the other is physical adsorption. The common absorbent is amine-based chemical solvents (commonly known as the amine method). Industry insiders engaged in carbon capture testing explain that amine-based chemical solvents are alkaline and, upon contact with factory emissions, form ammonium carboxylate rich in high-concentration carbon dioxide. The ammonium carboxylate is then heated and resolved in a stripping tower to obtain carbon dioxide of even higher concentration.
Although this method currently has a wide range of applications with high capture efficiency and purity, the process involves heating to resolve industrial flue gas containing a large amount of nitrogen, which implies a significant consumption of steam, an inevitable energy expenditure. A research report from Minsheng Securities points out that the most widely used alcohol amine absorbent in China can consume up to 4 GJ (gigajoules, a unit of energy consumption) to 6 GJ of energy per ton of carbon dioxide absorbed, equivalent to the consumption of 0.14 to 0.2 tons of standard coal.
Adsorption is simpler, utilizing the weak molecular forces, also known as van der Waals forces, on the surfaces of porous materials such as zeolites and activated carbon to capture carbon dioxide molecules. This process typically involves adsorption at low temperatures and high pressures, with release at high temperatures and low pressures. The aforementioned Icelandic Mammoth Factory employs this route.
Physical adsorption actually consumes more energy than chemical solvent absorption, as factories consume electricity. Therefore, it is best to be driven by new energy sources such as wind and solar power, geothermal energy, etc., otherwise, the costs will only be higher. Climeworks chose Iceland for its site because of the abundance of volcanoes and geothermal resources, and the underground basalt is suitable for storing carbon dioxide—this leads to a new question, should the captured carbon dioxide be utilized or stored permanently? How to conduct this "carbon business" is, in fact, the key to the sustainable operation of the entire chain.
Comment