Can a part that takes months to make be made in 10 days with 3D printing? Rocket
01
Another Milestone in Commercial Rocketry
At present, there are numerous new technological competition points in the commercial rocket industry, such as reusability and the application of liquid oxygen-methane propellants, among which 3D printing is not unfamiliar.
In the American TV series "Westworld," directed by Nolan, there is a scene where a massive 3D printing mechanical arm tears apart white material like threads, weaving back and forth. Distinct muscle lines, complex eye irises, and other human body parts gradually emerge from the mechanical weaving, and an NPC indistinguishable from a real person is born from the 3D printer. Of course, this is a work of science fiction. Although our current research and development technology can print some bioactive materials, it is far from reaching this level. However, in the field of industrial manufacturing, the capabilities of 3D printing cannot be ignored.
Generally speaking, 3D printing is used in the manufacturing of some rocket components, such as the rocket's nose cone, the thrust chamber of the attitude adjuster, and so on. No matter how "strangely shaped," they can be manufactured using 3D printing technology within a time frame of days.
There are even more radical examples, such as the American rocket design and manufacturing company Relativity Space. Their "Terran 1 (Terran One)" rocket, which was successfully launched in March last year but did not successfully enter orbit, includes 85% of its entire structural system (which can be simply understood as the rocket's shell) and nine engines, all of which are manufactured using 3D printing technology. It is claimed to be the world's first 3D printed rocket, and Terran 1 is also a liquid fuel rocket using liquid oxygen-methane as propellant, also designed with reusability in mind.
Advertisement
Terran 1 is currently the first 3D printed rocket.
SpaceX, the most famous in the commercial rocket field, although not as extreme as Relativity Space in utilizing 3D printing, is actually one of the pioneers and biggest supporters of using this technology in aerospace.In SpaceX's product lineup, components such as the turbine pump casing and fuel injector plate for the Raptor engine that powers the Starship, the thrust chamber, nozzle, and extension parts for the Merlin engine that powers the Falcon, as well as the rocket's heat shield, valves and fittings for controlling propellant flow, fairing components for protecting satellites and other payloads, the grid fins introduced in previous articles, and even the helmet visors of the spacesuits, are all manufactured using 3D printing.
"Traditional manufacturing is subtractive, where material is carved from a solid block or cast using molds, but 3D printing technology, also known as additive manufacturing, is quite the opposite," explained a business representative from铂力特, a domestic supplier of complete solutions for metal additive manufacturing. 3D printing is a manufacturing process that builds from points to lines, from lines to surfaces, and from surfaces to solids, using minimal material and allowing for high customization. Complex structural parts no longer require CAD design, optimization, and verification; a few parameter adjustments are all it takes.
In his view, rocket manufacturers are best suited for 3D printing technology for two main reasons: first, because metal 3D printing equipment is relatively expensive and only leading enterprises with financial support can afford to purchase it; second, because aerospace parts need to be lightweight while ensuring structural feasibility. If manufactured using traditional methods, they would need to be assembled from composite parts, which is not conducive to the manufacturing and assembly of reusable rockets and would inevitably lead to error rates affecting part usage.
"Structural components optimized through computer topology can only be made with 3D printing, such as complex load-bearing frames. 3D printing can remove every gram of unnecessary material to achieve optimal strength and can reduce parts that are on a scale of tens of thousands to just over a thousand," the aforementioned business representative explained.
02
Manufacturing New Rocket Parts in 10 Days
So, how are the metal components used on rockets printed? Taking the combustion chamber of a rocket engine as an example, the combustion chamber is where the rocket's liquid fuel and oxidizer burn and expand. The propellant is injected into the combustion chamber through an injector, then undergoes processes such as atomization, evaporation, mixing, and combustion to form combustion products, which are then expelled at high speed from the nozzle to generate thrust and propel the rocket into launch.During this process, the pressure inside the combustion chamber typically reaches 200 atmospheres (approximately 20 MPa), and the temperature can reach 3000 to 4000 degrees Celsius, so a cooling system is essential.
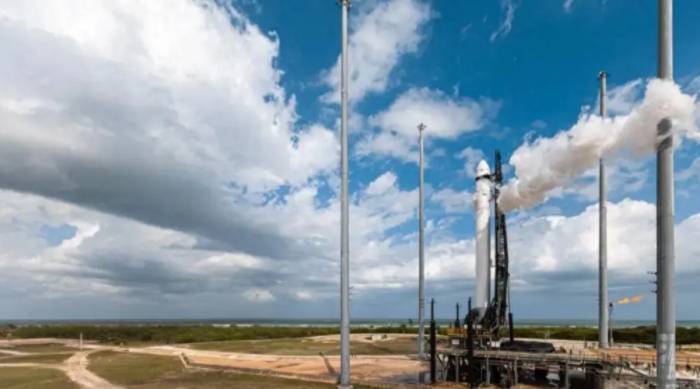
In 2015, NASA used a high thermal conductivity, high-strength copper alloy (designated as GRCop-84) to manufacture the combustion chamber lining and nozzle. After calculations with simulation software, to prevent excessive heating and rapid cooling, the combustion chamber lining required a "thin-walled channel" design, which refers to internal cooling channels. However, traditional manufacturing methods would struggle to meet the complex geometric design, so NASA opted to manufacture the combustion chamber lining using Laser Powder Bed Fusion (L-PBF) technology. The entire process took 10 days and 18 hours, printing 8255 layers, with the final structure consisting of over 200 complex and minuscule cooling channels between the inner and outer walls.
As we delve deeper into the application of 3D printing in the aerospace field, we can sense that after more than 40 years of development, the 3D printing industry chain has become quite mature. Common 3D printing typically uses materials like resin and plastic, while aerospace and defense enterprises generally require parts made from metals, carbon fiber, ceramics, and so on. New materials often require the support of new equipment and technology.
For instance, the copper alloy used by NASA was developed by the established American additive manufacturing solutions provider Sintavia, which created proprietary 3D printing modeling software, generated specific parameter sets, and compiled them for the printer. The actual printing was then accomplished using a printer from the German 3D printing equipment supplier EOS. Domestic companies, in response to the manufacturing industry's increasing emphasis on 3D printing applications, are also maturing, with suppliers like铂力特 emerging. However, there are still barriers in terms of patents.
From a technical standpoint, the 3D printing technology currently used in the aerospace field is mostly "Direct Metal Printing" (DMP), which starts with metal powder as the raw material and manufactures products layer by layer, fusing each layer of metal powder onto the previous one, resulting in parts with high strength and superior fracture resistance.
Direct Metal Printing can meet the diverse needs of rocket components.
Direct Metal Printing is further divided into three main categories: Powder Bed Fusion (PBF), Directed Energy Deposition (DED), and Ultrasonic Additive Manufacturing (UAM). We will delve into the specifics of these three printing technologies in subsequent articles, but for now, let's briefly discuss their respective advantages.
PBF is generally used for high-precision, geometrically complex parts, which are typically small to medium-sized components, such as the aforementioned combustion chamber lining; DED allows for large-scale additive manufacturing, suitable for the production of large-sized parts, like a large rocket nozzle that is 1.8 meters tall and 1.5 meters in diameter, and it can also serve a repair function; UAM can achieve true metallurgical bonding, making it suitable for multi-material composite structures or components with embedded elements.Regardless of the specific manufacturing process, any method that can quickly validate during the research and development phase, enabling rapid iteration of the design for reusable rockets, deserves our attention.
Comment