my country's heavy gas turbine breaks through 80 years of shackles, and aircraft
After more than 80 years of facing blockades and challenges, China has finally broken through the shackles of foreign technology.
01
The history of the blockade on cutting-edge technology that has lasted for nearly a century mainly stems from its high technological threshold and strategic importance. Heavy-duty gas turbine technology is hailed as the "pearl of the crown" in the mechanical industry, characterized by extreme technical complexity and strategic value.
The full name for gas turbines is gas turbine engines or combustion turbine engines. The term "gas turbine" can be a broad designation, with the basic principles being largely similar, including turbojet engines, among others.
The gas turbine engines commonly referred to usually pertain to those used in ships (primarily military warships), vehicles (usually large ones that can accommodate gas turbines, such as tanks, engineering vehicles, etc.), and power generation units. The difference from propulsion turbines lies in the fact that, in addition to driving the compressor, the turbine also drives a transmission shaft, which is connected to the vehicle's transmission system, the ship's propeller, or the generator, etc.
Advertisement
Based on output power, gas turbines can be categorized into three types: micro, light, and heavy-duty. Micro and light gas turbines can be derived from aviation engines, with power usually under 50MW, suitable for industrial power generation, marine propulsion, pipeline compression, tank locomotives, distributed power generation, and combined heat and power supply scenarios; heavy-duty gas turbines have a power output above 50MW and are mainly used as fixed power generation units on land, such as urban power grids.
Compared to micro and light gas turbines, heavy-duty gas turbines are core equipment for efficient energy conversion, clean utilization, and multi-field applications. They are an important symbol of an industrial powerhouse. Due to their extremely high design, manufacturing, and testing difficulties, as well as their significant economic, technological, and military value, they are major equipment that countries around the world are competing to develop.As one of the earliest countries in the world to develop heavy-duty gas turbines, the United Kingdom had already developed the G6 gas turbine in the 1950s. In the following decades, renowned heavy-duty gas turbines such as Olympus and Poseidon were successively introduced to the world. Even today, as the UK's national strength gradually declines, it still maintains a leading position in the field of heavy-duty gas turbines. The MT30 gas turbines currently used on the UK's two Queen Elizabeth-class aircraft carriers are the world's most advanced heavy-duty gas turbines, capable of propelling the 60,000-ton Queen Elizabeth-class carriers with just two units.
Companies such as General Electric (GE) in the United States and Siemens in Germany had already begun researching gas turbine technology before and after World War II, and have consistently followed a path of original innovation. This long-term technological accumulation has given them a significant technological advantage in this field.
For a long time, the cutting-edge technologies of heavy-duty gas turbine design, manufacturing, and testing have been entirely monopolized by a few companies such as Siemens of Germany, General Electric of the United States, and Mitsubishi of Japan. These companies not only dominate the technology and market but also further consolidate their monopolistic position through methods such as technology exchange in the market. As the core power source for large warships and heavy equipment, heavy-duty gas turbines have always been a focus of attention for various countries.
Since the 1980s, the world's most advanced large surface warships have basically adopted combined power units of gas turbines, such as the U.S. Navy's Arleigh Burke-class destroyers and Japan's Atago-class and Kongo-class destroyers. Due to various reasons, there has always been a significant gap between China's ship gas turbines and the international advanced level. The backward state of power in many fields has become the "bottleneck" restricting the development of large surface warships, and the technology was once controlled by only a few developed countries in the world. Advanced gas turbines are still restricted for export to China by Western countries.
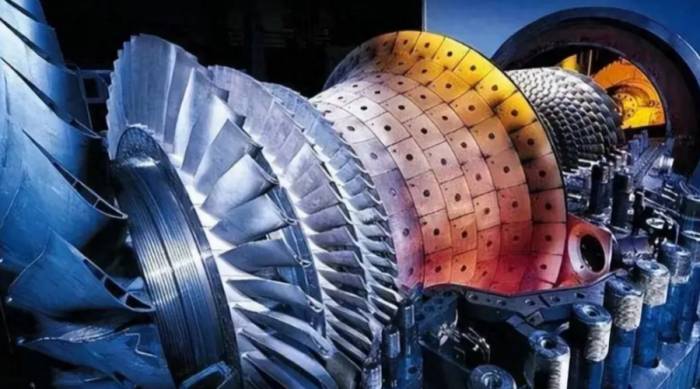
The most resented incident among the Chinese people is probably the purchase of General Electric gas turbines for the first ship of the 052 class, the "Harbin". In the early 1980s, the Chinese Navy decided to use gas turbines on the second-generation missile destroyers. At that time, the domestically developed models of gas turbines either could not meet the reliability requirements or had unsatisfactory performance in terms of power and efficiency. Therefore, it was decided to introduce models from abroad. General Electric's LM2500 was superior to the British equivalent in comprehensive performance, and in the mid-1980s, the United States promised to gradually transfer the technology of the LM2500, enabling China to gain the ability to imitate and produce the LM2500. Therefore, China decided to install the LM2500 gas turbines on the 052-class destroyers.
However, when the construction of the first ship of the 052 class, the "Harbin," began, things had already changed. The West reinstated the ban on the export of weapons technology and equipment to China, and the introduction of the LM2500 was obstructed. China only obtained four finished LM2500 units and one LM2500 prototype for training and experimentation. Judging from the situation at the time, it was already very difficult for China to obtain new ship-type LM2500 gas turbines, and technical authorization and transfer were also impossible. Even the subsequent major maintenance work for this model was no longer assisted by the American side.Breaking the blockade, the development of domestically researched heavy-duty gas turbines became a goal in the hearts of many researchers in the industrial field at that time.
Compared to Western countries, China's start in heavy-duty gas turbines was very late, even later than the start of aero engines. It was not until the late 1990s that China truly began a series of research and development efforts on domestic gas turbines. Before 2008, countries such as the United States, Russia, the United Kingdom, and Germany not only held the majority of the gas turbine market share but also possessed all the key technologies for producing gas turbines. As a latecomer, if our country wanted to manufacture gas turbines before, it had to import core components from Western countries and pay for peripheral technologies and technology licenses every year.
Even in the civilian market, Western countries imposed technological blockades on China, causing our country to rely on imitation, introduction, joint ventures, and other methods to obtain heavy-duty gas turbine technology for a long time.
02
Self-reliance and strength
Continuously breaking through foreign technological shackles
"If there is a lack of experts, cultivate oneself into an expert; if there is a lack of experience, try out experience."
The development of China's gas turbines originated from the assistance of the Soviet Union. In 1951, Soviet experts came to China to guide the development of the MiG-15 fighter jet, and Chinese experts first deeply understood its internal structure. Subsequently, the Soviet Union also provided technology for the MiG-17 fighter jet, helping China to achieve independent production and assembly.At the same time, China made progress in the development of steam turbines, and in 1953, with the assistance of experts from Czechoslovakia, we successfully developed a 6-megawatt power generation steam turbine. However, after the Sino-Soviet relations deteriorated in 1959, gas turbine technology became isolated from the outside world, with both the Western bloc and the Soviet bloc keeping this technology strictly confidential.
It was not until the late 1990s that China truly began a series of research and development efforts on domestic gas turbines, with the foundational technology mainly derived from the relatively weak Soviet Union and Ukraine. Despite the late start, China managed to acquire numerous advanced gas turbines from abroad, the most famous of which was the UGT-25000 from Ukraine. By reverse-engineering these mature reference samples, China subsequently manufactured several domestic heavy-duty gas turbines.
China also successfully developed the QC-280 gas turbine by introducing the UGT-25000 gas turbine technology from Ukraine, achieving a 100% localization rate for this gas turbine. This marked a new chapter for us.
Entering the 21st century, with the progress of projects such as the West-East Gas Pipeline, coupled with the large-scale import of liquefied natural gas, our country regained the momentum for developing heavy-duty gas turbines. However, at this time, China also faced strict technological blockades from foreign companies. In order to close the technological gap in the shortest time possible, China adopted a market-for-technology model, importing a batch of more advanced heavy-duty gas turbines. But this did not change the situation of being at the mercy of others. Foreign engineers refused to allow our technical personnel to approach the equipment throughout the process, and the domestically produced complete machines were not only restricted to domestic sales but also required the employment of foreign engineers for maintenance, which undoubtedly hurt the self-esteem of personnel in related industries.
Reading literature, researching materials, translating foreign documents, and learning in power plants. "If there is a lack of experts, cultivate oneself into an expert; if there is a lack of experience, try out experience." This was the belief of the engineers at Dongfang Electric in those years.
In the 1980s of the last century, the people of Dongfang created the first generation of Dongfang "self-respect machine" — a 300,000-kilowatt steam turbine. Today, the baton of the new era "self-respect machine" has been passed to a new generation of Dongfang people. In 2009, a young team, inheriting the entrepreneurial spirit of their predecessors, officially embarked on the path of independently developing the F-class 50-megawatt heavy-duty gas turbine (referred to as "G50 gas turbine").
From 2001 to 2007, over a period of six years, China introduced over 60 sets of E-class and F-class heavy-duty gas turbines with a total capacity of 20 million kilowatts through four consortiums: Harbin-GE, Dongfang-Mitsubishi Heavy Industries, Shanghai-Siemens, and Nanjing-GE. Through this process, the four major domestic heavy-duty gas turbine manufacturing enterprises mastered the manufacturing of cold-end components and the assembly of the whole machine for E-class and F-class heavy-duty gas turbines. However, the core design and manufacturing technology for hot-end components were still monopolized by foreign parties, and they had to rely mainly on imports.
It was not until 2019 that China completed the manufacturing of the first-stage moving blades, stationary blades, and combustion chambers for the F-class 300MW gas turbine. The first F-class 50MW heavy-duty gas turbine prototype of Dongfang Electric Corporation successfully passed the whole machine ignition test, indicating that China has broken through a series of "bottleneck" core technologies, initially obtained the manufacturing technology capability for high-temperature components of heavy-duty gas turbines, and preliminarily possessed the full-process capability for independent research and development of E-class/F-class heavy-duty gas turbines.Looking at the progress of domestication of key core components of heavy-duty gas turbines, taking the market mainstream F-class heavy-duty gas turbines as an example, the rate of domestication of production and manufacturing technology for heavy-duty gas turbines in China has significantly increased. The domestication rate of the number of gas turbine components in China can reach 80%-90%, but the domestication proportion of the value of gas turbine components is still less than 70%. Only by working hard can we achieve the catch-up and surpassing of technology.
03
The 055s will no longer have any weaknesses
After the efforts of several generations of people from many enterprises, our country has started to make significant progress in the field of heavy-duty gas turbines.
In the process of domesticating the UGT-25000, it was not only the introduction of technology but also the digestion, absorption, and improvement. Drawing on the equipment use experience of the LM25000, our country carried out the first phase series of improvements on the UGT-25000. Through the efforts of the 703rd Research Institute of China Shipbuilding Heavy Industry, Xi'an Aero-Engine Group, and Harbin Power Group, the first domestically produced UGT-25000 was trial-produced in 2004, with performance comparable to the original Ukrainian-produced units, and the domestication rate reached more than 60%.
The second phase of domestication work mainly aimed to increase the domestication rate to more than 95%, basically achieving the domestication of materials and processes. At present, the fully domesticated unit - QC280 has been mass-produced, providing the necessary power support for the construction of China's 052D and 055 new generation surface warships.
In the mid-to-late 1990s, the technological breakthrough of our country's "Taihang" turbofan engine brought greater possibilities for the development of our country's gas turbines. The first type of "Taihang" modified gas turbine was the QD70, with the marine version being the QC70, which is China's first 7000-kilowatt gas turbine. It began development in 1996 and was put into use in 2006.
In response to the needs of large and medium-sized surface warships, China has also launched the QC185 gas turbine with a power of 25,000 horsepower based on the "Taihang" turbofan engine. As a medium-power gas turbine, the QC185 can serve as the main power of the destroyer and escort ships, which also marks another key step for our country on the path of independently developing and producing shipborne gas turbines.Continuous breakthroughs mean that Chinese destroyers are no longer held back by the constraints of heavy-duty gas turbines.
In 2015, China overcame the manufacturing challenge of rhenium metal single-crystal blades, significantly enhancing gas turbine technology to the level of the United States and Russia. Subsequently, China successfully developed gas turbines such as Taihang 110, GT25000, and CGT40. The latest 50-megawatt F-class gas turbine operates at a lower temperature and has a high thermal efficiency, with performance approaching that of the H-class.
Currently, the most widely used gas turbine in Chinese naval vessels is the QD280 model, derived from the domestic UGT-25000. The R0110 gas turbine developed by China this time surpasses any previously owned gas turbine in both technology and power. Under ISO conditions, this gas turbine can output 114,500 kilowatts of power, making it highly suitable for use in aircraft carriers.
At present, China's two domestically produced aircraft carriers are still using steam turbines for propulsion. Once they are equipped with gas turbines, their power will be greatly enhanced, allowing them to navigate at high speeds on the sea, improving their maneuverability, and even reducing the restrictions on the takeoff of carrier-based aircraft.
From being blocked to imitation to self-sufficiency, China's development in heavy-duty gas turbines has been rapid. It has achieved a breakthrough from "0" to "1," enabling China to have its own "heart" and solving issues such as China's "heart disease," and the era of being "held back" has also come to an end.
04
Countermeasures
China's controlled exports already include gas turbines.From military to civilian applications, through concerted efforts, China's heavy-duty gas turbines have finally broken through to reach the global mainstream level, further narrowing the gap with GE and Siemens. This has allowed the country's energy-critical equipment, aircraft carrier gas turbines, and aviation-modified engines to begin a counterattack against Western equipment blockades.
At the end of February, China overcame the world's mainstream high-power heavy-duty gas turbine technology, developing a 300-megawatt F-class heavy-duty gas turbine, with the first prototype successfully assembled and rolled off the production line in Shanghai. In July, China's first independently developed 15-megawatt heavy-duty gas turbine, the "G15," was assembled and rolled off the production line in Deyang, Sichuan, providing support for China to accelerate the formation of its own gas turbine spectrum and optimize its energy structure.
According to public information, in March 2023, China's first F-class 50-megawatt heavy-duty gas turbine with independent intellectual property rights, the G50 (hereinafter referred to as "G50"), officially entered commercial operation at China Huadian Qingyuan Power Plant, achieving a breakthrough from "0" to "1" for China's independent heavy-duty gas turbines.
It is worth mentioning that in May of this year, the Ministry of Commerce, the Ministry of Science and Technology, and the Ministry of Industry and Information Technology of China jointly issued an announcement to control the export of products and technologies such as gas turbines.
As an important military equipment, the main material of gas turbines is aviation gas turbines. If they are stolen and leaked to hostile forces, it would pose a significant threat to our country's strategic security. Therefore, China's export control on gas turbines is to maintain national security.
The export of these sensitive technologies has a significant impact on our country's security and interests. China has also controlled the export of rare earths, which are an important industrial element and an irreplaceable resource. However, China's rare earth resources account for more than 60% of the global total, which to some extent allows our country to rely on rare earth resources as a powerful weapon while developing.
It is precisely the adoption of the export of these sensitive and important technologies and the implementation of export controls on these key technologies that have greatly promoted the formation of our country's industrial chains, prevented the proliferation of sensitive technologies, and are conducive to maintaining our country's core competitiveness in the world!
Comment